Climate change is one of the most urgent and intensifying challenges the world faces today. We aim to tread lightly and become a Net-Zero business by investing in reducing our impact on the planet and helping our suppliers to operate in a responsible way.
This is how we reduce our carbon footprint, eliminate waste at source, recycle more, and responsibly manage issues like chemcials and water. By sharing what we learn, we can support our global supply chain to measure and mitigate their impacts as well.
climate
At DM’s we recognise that rapid action is needed to respond to the climate crisis. It is a global challenge that already affects us all and will do so increasingly.
As Dr. Martens brand custodians, we have a responsibility to think about the future impact of our decisions and take bold steps as we move towards our long-term vision of a Net-Zero business.
We have set science-based Net-Zero targets which were validated by the Science Based Target Initiative (SBTi) in October 2023. Our targets include both near and long-term emissions reduction targets, to help us to transform our business and collectively prevent the most severe impacts of climate change. Leather accounts for a significant portion of our total emissions profile so we also have set specific leather emissions reduction targets according to the Forest, Land and Agriculture (FLAG) Guidance:
Dr. Martens commits to Net-Zero GHG emissions across the value chain by FY40.
Near-Term Targets
- Scope 1 and 2:
- Reduce absolute scope 1 and 2 GHG emissions 90% by FY30 from a FY20 base year.
- Scope 3:
- Reduce absolute scope 3 GHG emissions 30% by FY30 from a FY20 base year.
- FLAG (Forests, Land and Agriculture): reduce absolute Scope 3 FLAG GHG emissions 30.3% by FY30 from a FY20 base year.
Long-Term Targets
- Scope 1 and 2:
- Maintain at least 90% absolute scope 1 and 2 GHG emissions reductions from FY30 through FY40 from a FY20 base year.
- Scope 3:
- Reduce absolute scope 3 scopes GHG emissions 90% by FY40 from a FY20 base year.
- FLAG: reduce absolute scope 3 FLAG GHG emissions 72% within the same timeframe.
Other Targets
- Increase active annual sourcing of renewable electricity to 100% by FY26, and to continue sourcing 100% renewable electricity through FY30.
- Dr. Martens commits to no deforestation across its primary deforestation-linked commodities, with a target date of 2025
Our emissions reduction strategy
Our Planet, Product, People sustainability strategy captures the areas we are working on as we progress with our Net-Zero by FY40 target. We know we have a part to play that looks beyond our direct impact. As a footwear company, most of our climate impacts lie within our global supply chain. That is why in addition to our ongoing efforts to reduce our direct emissions, we will also work closely with our suppliers.
Here are some of the opportunitites we are exploring to help us reduce our emissions:
- Souring renewable energy at our stores, offices, distribution centre and MIE Factory
- Improving energy efficiency through HVAAC optimisation and installing LED lighting and smart meters
- Transitioning to lower impact materials such as bio-based alternatives
- Increased circularity including design, maximising product lifespan and exploring sustainable solutions for end-of-life disposal
- Scaling up our repair and resale business models
Check out the Climate section of our Sustainability Report for more information.
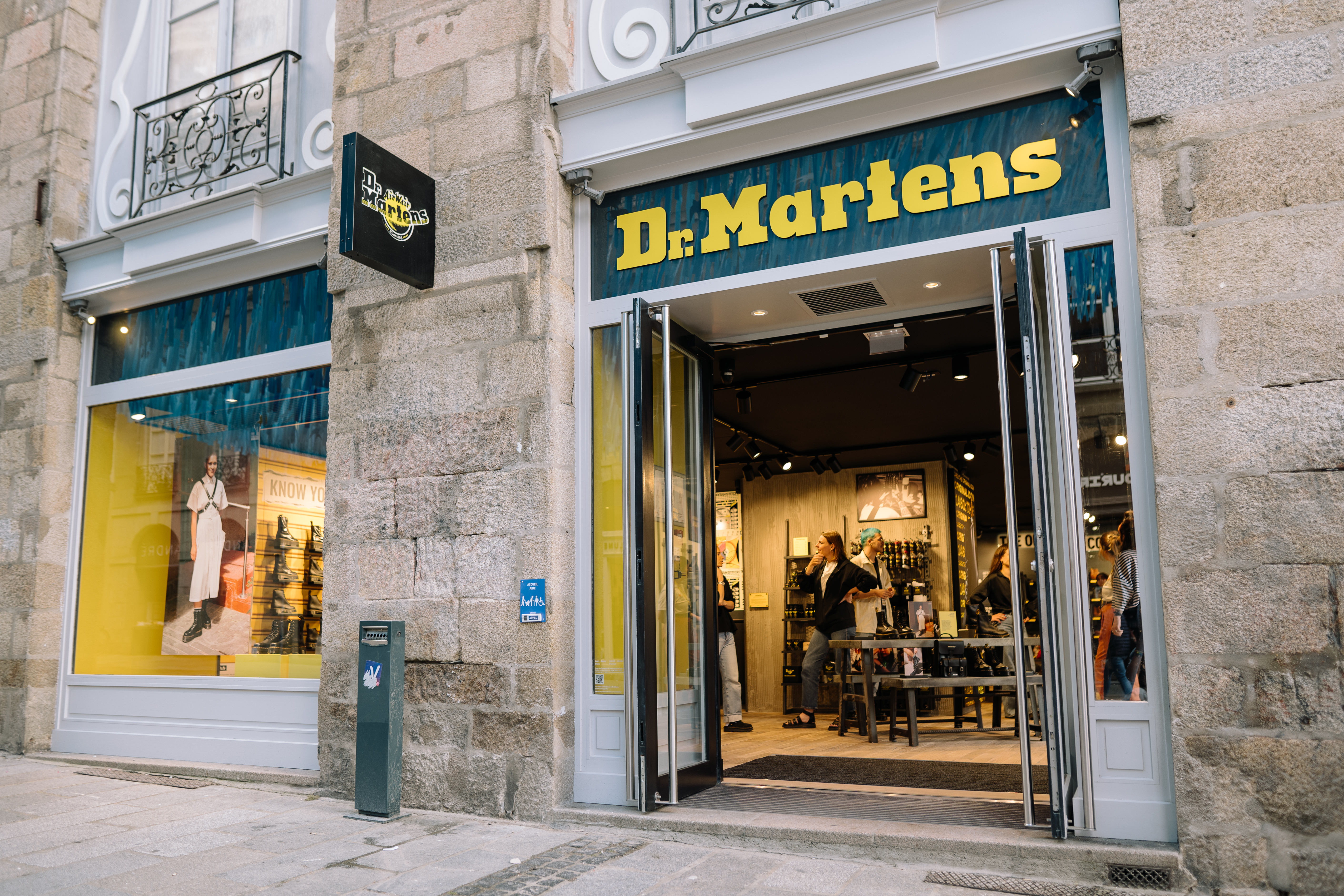
Our operations
We believe the places we work should be a reflection of our company values - being a responsible brand starts with our owned and operated facilities.
- Around 93% of the electricity supplying our owned and operated sites across Europe (including the UK) is from renewable sources, and almost half of energy consumption globally. We continue to work towards achieving this across all our owned and operated sites globally.
- Our UK distribution centre and Made In England factory are zero waste to landfill. We are also working with our Tier 1 suppliers to achieve zero waste to landfill in our supply chain too.
- The Netherlands distribution centre and our UK distribution centre were designed with sustainability in mind and achieved a BREEAM rating of Very Good. Our Carnaby Street store in London is also BREEAM certified. BREEAM provides a holistic sustainability assessment framework for buildings and infrastructure, ensuring that projects meet sustainability goals and continue to perform optimally over time.
Made in England
Cobb’s Lane in Wollaston, UK, is the birthplace of the first pair of Dr. Martens boots. To this day, it remains the location where our Made in England (MIE) products are manufactured .
Our MIE site has been ISO 14001 certified since 2021. ISO 14001 is the internationally recognised standard which enables organisations to monitor and manage their environmental impacts in a systematic way and demonstrates a commitment to environmental protection above and beyond legal requirements.
We want to lead by example, which is why we are also supporting our Tier 1 suppliers to gain environmental certification standards by 2025.
Sustainable Store Design
Our retail environment is the platform for our brand vision, our values and space where our community can come together.
We are working to adopt solutions which bring sustainability into the retail environment such as utilising sustainable materials in our stores, including reconditioned shop fixtures and bespoke recycled materials.
Global supply chain
Our global supply chain consists of manufacturing sites and distribution centres. As well as manufacturing our products in the UK, most of our footwear and accessories are produced in the factories of our trusted partners across Europe and Asia. We have fully mapped our Tier 1 and Key Tier 2 suppliers.
This disclosure accounts for all of our active Tier 1 footwear suppliers at the time of publishing and is reviewed and updated annually.
To learn more about our CSR programme in our supply chain, check out our most recent Sustainability Report, or visit People.
Supplier environmental standards
Our Environmental Standards set out our expectations for our suppliers’ environmental management. We monitor our key suppliers against these standards and their environmental performance through our ongoing supplier monitoring programme. We also monitor our key suppliers’ energy, water, waste and chemicals use on a quarterly basis.

LAND, BIODIVERSITY AND ECOSYSTEMS
We want to build a supply chain that is resilient and responsible. To do this we must understand the potential implications of climate change on our business as well as working to protect and restore nature.
Cattle farming continues to be a driver of deforestation. That is why we are working closely with our suppliers to ensure our supply chain is deforestation free, particularly focussing on leather. We have also started to develop a regenerative agriculture strategy which aims to provide positive environmental and social impacts, such as improving farmer livelihoods, soil health, water cycling, biodiversity and animal welfare. Regenerative agriculture can also increase farm and supply chain resilience to risks such as climate change.
Our suppliers are expected to meet our environmental standards for water consumption and wastewater disposal while manufacturing our products. Leather tanning is a key impact area for water use and wastewater emissions. We require our tanneries to be compliant with the Leather Working Group (LWG) audit protocol, which sets out requirements for more responsible water consumption.
WASTE
We work closely with our suppliers to minimise waste production through initiatives such as design optimisation. We also collect waste data from our suppliers to help us better understand our indirect waste impacts, particularly for leather and PVC. We use these insights to manage waste disposal in the supply chain as we work towards diverting waste from landfill. We also encourage waste disposal methods that are higher up the waste hierachy, for example recycling and reuse.
Read more about how we are tackling waste in our sustainability report as we work to minimise waste and ensure zero waste to landfill by 2028.
RSL and Chemical management
Restricted substances are chemicals and substances which have been banned or restricted for various reasons such as health and safety and environmental concerns. The purpose of a restricted substances list (RSL) is to reduce the use of hazardous substances in the supply chain. Testing methods are used to verify if a chemical is present and if so, ensure it is below the restricted level.
Dr. Martens General Material Requirement Policy (GMRP) is part of Dr. Martens RSL programme and is key to ensuring that our products comply with all relevant product safety legislation and requirements. The GMRP is shared with and signed by our Tier 1 and key Tier 2 suppliers each year. It is reviewed and updated annually and is aligned with the legal testing requirements in all our operational regions (UK, EU, US, China, Japan and Korea) including REACH legislation and California Proposition 65, which is considered the most stringent chemicals legislation worldwide. We are committed to continuing to be compliant with the tightest chemical regulations identified worldwide through a best practice chemical management system.
We use third-party testing labs to test products against the highest applicable requirements for the markets they are sold into. All of the testing labs we work with are pre-approved by Dr. Martens so we only work with trusted testing partners. Every new material and component type in our products goes through a rigorous testing programme each season to ensure it is compliant. Random products are selected from the production line by Dr. Martens Quality and Compliance team. As well as a comprehensive testing programme for our components and raw materials, we also carry out seasonal rip down (finished product) testing, where products are shredded and the individual components tested. If a product or material should fail a test for compliance reasons, an investigation is launched immediately to remediate the failure.