We believe the most responsible thing we can do is to maximise the longevity of each pair through the creation of timeless, hardwearing and repairable footwear.
We’re adopting more sustainable and traceable materials without compromising on quality, as we move towards our product lifecycle being regenerative and circular.
Materials
The materials we use not only underpin the durability, look and feel of our footwear, they also influence the lifecycle impacts of our products. We are developing more sustainable materials for the future, such as bio-based alternatives, which supports our commitment for all our footwear to be made from sustainable materials by 2040.
We have developed a framework to ensure materials selected consider all our sustainability requirements, rather than only looking at one aspect. We have called this our DRP Sustainable Materials Criteria, which evaluates if materials are Durable, Recycled, Renewable and/or Regenerative and Produced responsibly. These definitions act as the foundation for our efforts as we work towards meeting our sustainable materials targets.
DURABLE Durable materials are paramount to ensuring Dr. Martens products reach their maximum useable life. |
Durability is a core design principle for us, ensuring all products are designed and built to maximise the length of time they can be worn. This means materials must meet our quality and performance standards and align to our sustainable design criteria and timeless brand aesthetic. |
RECYCLED/ RENEWABLE/ REGENERATIVE Sustainably sourced materials lay the foundations for more sustainable products. |
Materials must be from credible recycled, renewable or regenerative sources. For recycled, this means material created from post-industrial or post-consumer recycled content. We strive to maximise recycled content without compromising durability. For non-recycled content, materials should be sourced from renewable sources that implement regenerative practices wherever possible. |
PRODUCED RESPONSIBLY Sustainable materials are manufactured using environmentally and socially sustainable practices. |
All material production must be underpinned by responsible practices, exemplified by our Supplier Code of Conduct, Workplace and Environmental Standards. This includes ensuring:
|
We are already using materials across our product range which meet our sustainability criteria. We aim to only source from Leather Working Group (LWG) certified tanneries, our standard heel loops are made from 100% post-consumer recycled polyester, and high-performance recycled materials are also being incorporated into our other componentry like laces and linings. We are also working to develop new materials where suitable ones do not already exist, such as bio-based outsoles.
Click on the + below to find out more about some of the main materials we use.
Leather is a key material for us. To support our ambition to leave things better than we found them, we are focussing on sourcing traceable, deforestation-free leather and exploring regeneratively sourced leather.
The raw material used to make the leather we use originates as a by-product of the food industry. We specify all the leathers used in our products from selected tanneries and aim to only work with Leather Working Group (LWG) certified tanneries. The tanneries that we work with are assessed for a number of factors, including their environmental and social responsibility to ensure they meet our high standards. It is also important we investigate and invest in leather alternatives, which forms part of our approach to achieving Net-Zero emissions.
We are a member of the Leather Working Group (LWG)
The LWG is a collective of tanneries, brands, suppliers, technical experts and non-governmental organisations (NGOs), whose aim is to raise environmental standards throughout the leather industry. LWG tanneries are audited on their environmental performance and are certified as Gold, Silver, Bronze or Audited, depending on their performance.
The LWG audit protocol assesses tanneries across key areas including energy consumption, water usage, air and noise emissions, waste management, health and safety, chemicals management, effluent treatment (which is aligned to the ZDHC wastewater requirements) and the traceability of material through the leather supply chain. Tanneries are now also required to have a recognised social audit. More information about the LWG audit protocol can be found on the LWG website.
The LWG has contributed to greater efficiency across the global leather supply chain, resulting in better environmental performance across the whole industry. This is why we are proud to work with tanneries committed to improving their processes and minimising their impacts. For the SS25 and AW25 seasons, 100% of our upper leather came from LWG certified tanneries.
Leather traceability
We have set ourselves the target to achieve 100% leather traceability to the abattoir by 2024. Although the hides we use for leather are sourced from cattle reared for the food industry, traceability is essential to ensure that our products are not linked to deforestation or other negative environmental, social or animal welfare impacts. Despite traceability being so important for responsible leather use, it is an ongoing challenge that requires industry-wide collaboration.
In FY25, we undertook an exercise with a third-party which identified that 97% of our leather is traceable back to the abattoir for the AW24 and SS25 seasons. This provided greater insight into our leather purchases and enhanced our visibility of the specific abattoirs which supply leather to our tannery partners.
Achieving this is only the beginning of our traceability journey, which will enable us to safeguard our leather supply chain from the risk of deforestation and other negative environmental impacts. Check out the leather section of our Sustainability Report for further updates on our progress. The LWG audit also scores tanneries on how much of the leather is traceable through their supply chain. We take this score into account when we select our tannery partners.
The LWG and its community are working with NGOs and other organisations to further enhance the LWG Audit Protocol in terms of traceability. The group is also inputting into further work to enable greater transparency throughout the leather supply chain to progress against areas of particular importance or concern, such as deforestation.
Animal Derived Materials Policy
We have an Animal Derived Materials Policy which sets out our full standards regarding animal derived materials. This includes the materials we do not use, like fur, and recognises the five freedoms as a guiding standard for animal welfare. It also specifies that our shoe care products must not be tested on animals.
Today, the majority of our outsoles are made from an alloy of PVC, a durable and commonly used plastic. Granules are melted and moulded into shape to create our famous Dr. Martens air-cushioned sole. Very little waste is produced from the moulding process because the waste PVC material can be recycled back into the production line.
The soles of all our Original products are oil and fat resistant. All our soles offer good abrasion and slip resistance, while the air pockets provide comfort and shock absorption.
To attach the sole, a PVC welt is first stitched to the upper of the boot. The welt and sole are welded together at a temperature in excess of 650°C using a hot blade and pressurised rollers that force the components together. Once cooled, the two components form one piece of PVC and the sole has been attached without the use of adhesives.
The use of PVC as one of our materials ensures our products will stand the test of time. As PVC is largely derived from fossil fuels, we are investing in research and development as we aim to achieve our target to remove fossil-based chemicals from our products by 2035, as well as our target for all our footwear to be made from sustainable materials by 2040.
We are committed to developing lower-carbon alternatives to our high impact materials, like leather and PVC, as we work towards achieving our long-term Net-Zero and sustainable materials commitments.
In 2024 we launched our first products made from reclaimed leather, an innovative material developed to help address leather waste. Named ‘Genix Nappa’, the reclaimed leather material is made from recycling leather offcuts into a soft, lightweight material, without compromising on our renowned durability. Approximately 50% of the material is made from recycled pre-consumer leather fibres, with a synthetic textile core and water-based polyurethane (PU) topcoat. We have found that this material results in an 80% reduction in carbon emissions compared to conventional leather.
We continue to test and develop a range of materials such as bio-based vegan upper alternatives and bio-based PVC. We won’t compromise on our high durability standards so we follow rigorous testing to ensure these alternative materials meet our aesthetic and performance standards and sustainability criteria. Check out our sustainability report to find out the latest updates on our alternative materials development programme.

Our shoebox is fully recyclable, made from 100% FSC recycled CARDBOARD
Packaging
By 2028 we are aiming for 100% of our packaging to be made from recycled or other sustainably sourced materials.
Most of the packaging we use is to protect and transport our products in our supply chain. We are working towards several improvements, such as sourcing more packaging with a sustainable certification (such as FSC), discontinuing non-recyclable items, and increasing the recycled content.
We are also taking regional best practice and introducing this elsewhere in our supply chain. For example, Hong Kong and China informed a cardboard reuse initiative in our UK and US distribution centres. We have also reduced the fibre content in our standard cardboard shoe box by 25% and reduced the plastic content in our ecommerce shipping bags by approximately 50%, without compromising product protection.
Lifecycle
Our products are iconic, timeless and durable. We are building on our proud heritage by working to prolong the life of our products and developing end-of-life solutions for our products. We want to support our wearers to keep their boots on their feet for as long as possible through care, repair and resale. This is why we’re committed to offering options and guidance for our wearers to maximise the useable life of their footwear by 2025.
But even the most loved boots will one day reach the end of their useable life. So we’re also working towards developing sustainable end-of-life options, like material segregation and recycling, for all our products by 2040. All of this is helping move our business towards a more circular model.
Repair: We’ve partnered with The Boot Repair Co. in the UK to offer our consumers authorised repair for their DM’s footwear and accessories. Through this service, we breathe new life into old footwear to keep them going for longer. Find out more here.
Resale: Resale is the next step forward on our journey to help our wearers make the most of their DM's products. Our resale schemes repair and resell second-hand DM's footwear and accessories.
You can find US resale, ReWair, here.
You can find UK resale here.
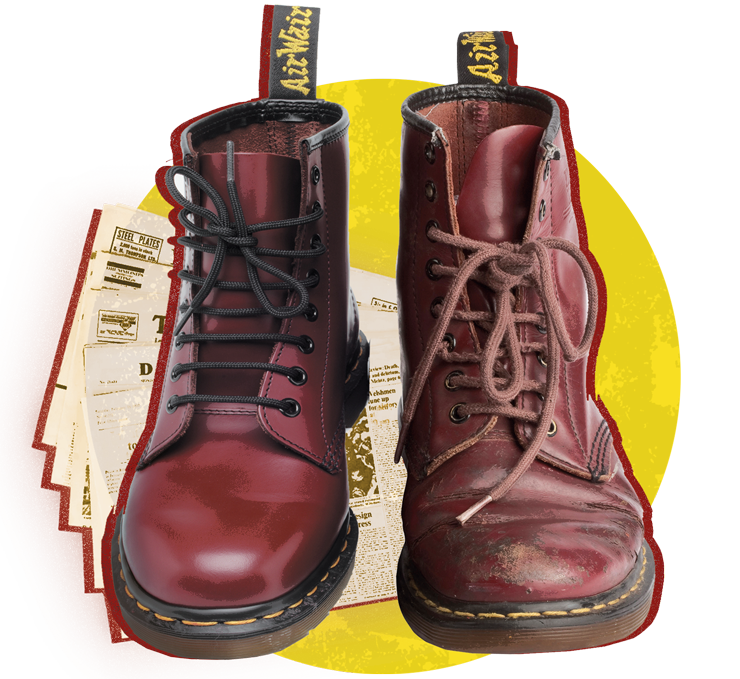
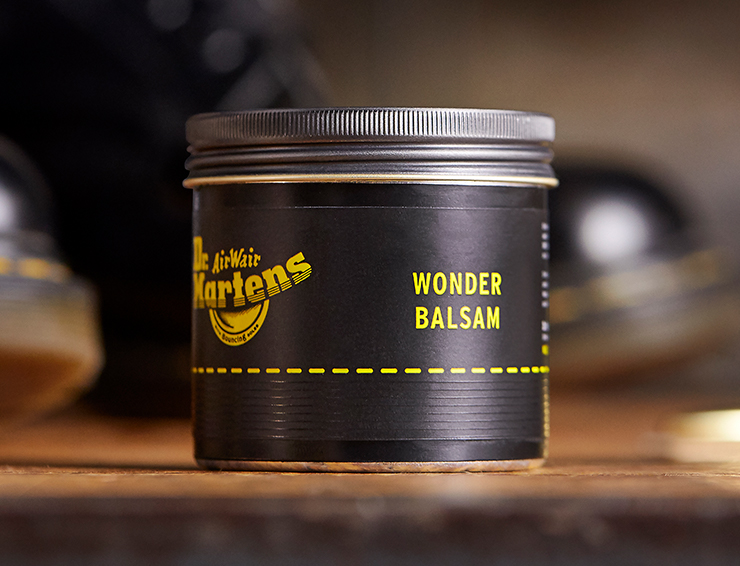
Durability and care
One of the most effective ways to reduce the environmental footprint of a product is to prolong its life. Research by Waste and Resources Action Programme (WRAP) has shown that increasing the lifespan of clothing by only nine months could reduce its annual carbon, water and waste footprint by 20–30%.
The timeless design and durable construction of our products mean they stand the test of time when cared for properly - but even tough shoes need looking after.
Learn how to maximise their life and care for your boots by following the links below: